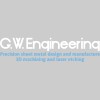
GW Engineering is a precision sheet metal, milling and turning sub-contractor and based in Trowbridge, Wiltshire with 30 years experience in the design & manufacture of enclosures, cabinets, racks and machined parts mainly for industrial equipment. We have the latest Amada CNC machine tools for punching, laser cutting and folding and HASS CNC machines for milling and turning.
We work in steel, stainless steel, aluminium, copper, brass. In addition, we have facilities for laser cutting plastic and laser etching plastic and metal using our Trotec Speedy 300 laser. MIG, TIG and spotwelding (including aluminium), a wide range of inserts and pop rivets are used for product assembly and we offer painting, plating and silk screen printing.
Solidworks and Inventor are used for product design where material use, ease of assembly, appearance and function are considered in parallel to minimize product costs and development lead times. Interesting examples can be found in Case Studies. We are constantly looking to improve competitiveness and customer service through many innovations which can be viewed in News.
We work in steel, stainless steel, aluminium, copper, brass. In addition, we have facilities for laser cutting plastic and laser etching plastic and metal using our Trotec Speedy 300 laser. MIG, TIG and spotwelding (including aluminium), a wide range of inserts and pop rivets are used for product assembly and we offer painting, plating and silk screen printing.
Solidworks and Inventor are used for product design where material use, ease of assembly, appearance and function are considered in parallel to minimize product costs and development lead times. Interesting examples can be found in Case Studies. We are constantly looking to improve competitiveness and customer service through many innovations which can be viewed in News.
Services
Sheet metal design and manufacture is an important part of our business and our team can be relied upon come up with low cost, functional, attractive designs.
Development is done in 3D using Solidworks or Inventor to ensure all internal parts such as PCB's and power supplies fit with the metalwork.
As work progresses, we supply "3D Viewer" files for customer approval before making the 1st-off prototype.
The models produced are 100% accurate and 2D manufacturing drawings and CNC programs are generated directly from the models ensuring integrity of the data throughout the design and manufacturing process.
Development is done in 3D using Solidworks or Inventor to ensure all internal parts such as PCB's and power supplies fit with the metalwork.
As work progresses, we supply "3D Viewer" files for customer approval before making the 1st-off prototype.
The models produced are 100% accurate and 2D manufacturing drawings and CNC programs are generated directly from the models ensuring integrity of the data throughout the design and manufacturing process.
We design and manufacture assembled sheet metal products such as enclosures, 19 racks and cabinets complete doors, drawers, locks and casters or supply individual parts for assembly by the customer.
We do not currently assemble electronics into enclosures.
We also manufacture "flat pack" products for on-site assembly which can save considerably on storage and transportation costs.
If you would to be kept up to date with developments at GW Engineering, please sign up for our regular Newsletter below.
We do not currently assemble electronics into enclosures.
We also manufacture "flat pack" products for on-site assembly which can save considerably on storage and transportation costs.
If you would to be kept up to date with developments at GW Engineering, please sign up for our regular Newsletter below.
Punching is used on thinner materials with simple profiles and on parts with 'forms' such as dipples and louvres.
Punching compliments the work done on our Amada LCG-3015 fiber laser.
Design parts using hole sizes for which we have tools to avoid the need to purchase special tools.
If in doubt, ask for a tool list.
Ensure holes are more than 2 x material thickness away from a component edge to avoid 'blowout'.
Punching compliments the work done on our Amada LCG-3015 fiber laser.
Design parts using hole sizes for which we have tools to avoid the need to purchase special tools.
If in doubt, ask for a tool list.
Ensure holes are more than 2 x material thickness away from a component edge to avoid 'blowout'.
We have an Amada LCG-3015 AJ 2kW fibre laser with a working range of 3000mm x 1500mm with sheet load/unload facilities and a nitrogen generation plant.
This machine is fast, flexible and since no tooling is required, sheet usage is optimised and job change over times minimised for maximum efficiency.
It is now our main production machine complimented by our Amada CNC punching machine for jobs with forms such as dimples.
The machine can cut reflective materials such as copper and brass and because the assist gas is mainly nitrogen, discoloration and oxidization of sheet edges is eliminated so no further preparation is required for painting or plating.
This machine is fast, flexible and since no tooling is required, sheet usage is optimised and job change over times minimised for maximum efficiency.
It is now our main production machine complimented by our Amada CNC punching machine for jobs with forms such as dimples.
The machine can cut reflective materials such as copper and brass and because the assist gas is mainly nitrogen, discoloration and oxidization of sheet edges is eliminated so no further preparation is required for painting or plating.
For high speed automatic folding we have an Amada EG6013AR Robotic Bending Cell for high mix, low volume, complex parts.
We achieve highly accurate, repeatable folds and generally work within 0.2mm across multiple faces.
The machines have settings which can be adjusted to accommodate variances in materials between batches without modifying the program.
We achieve highly accurate, repeatable folds and generally work within 0.2mm across multiple faces.
The machines have settings which can be adjusted to accommodate variances in materials between batches without modifying the program.
Reviews
Be the first to review G W Engineering.
Write a Review