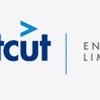
Established in 1991, Westcut Engineering Limited has grown to become an established and trusted engineering supplier to leading manufacturing companies. Initially a specialist tool making manufacturer, Westcut added hydraulic presses and water jet cutting to its operation and has ensured that the business tracks and invests in modern technology to offer its customers the most efficient manufacturing methods available.
Services
Our advanced waterjet cutting machine allows us to produce complex shapes, in a broad range of materials, to extremely tight tolerances.
Producing a 0.8 mm jet of water at 60,000 PSI, the water-jet machine allows us to cut intricate shapes to tolerances of +/- 0.2 mm.
The process also allows for extremely flexible quantity requirements to be met, from rapid prototyping for development work to full volume production.
Regardless of quantity requirements, waterjet technology cost-effectively produces components to a consistent quality standard.
Producing a 0.8 mm jet of water at 60,000 PSI, the water-jet machine allows us to cut intricate shapes to tolerances of +/- 0.2 mm.
The process also allows for extremely flexible quantity requirements to be met, from rapid prototyping for development work to full volume production.
Regardless of quantity requirements, waterjet technology cost-effectively produces components to a consistent quality standard.
Our range of Wire Erosion and Plunge type EDM machines compliment the services provided by our in-house tool room.
These machines are used in the production of precision tooling that we manufacture and in the production of extremely accurate shapes that cannot be cost-effectively produced by any other method.
Industries, where we have found our wire erosion machining can offer major benefits due to the very close tolerances that can be maintained include aerospace, pharmaceutical, oil and gas, nuclear, motorsport, military and defence.
These machines are used in the production of precision tooling that we manufacture and in the production of extremely accurate shapes that cannot be cost-effectively produced by any other method.
Industries, where we have found our wire erosion machining can offer major benefits due to the very close tolerances that can be maintained include aerospace, pharmaceutical, oil and gas, nuclear, motorsport, military and defence.
Our wide range of hydraulic presses are capable of meeting the majority of pressing and forming requirements.
With a dedicated and experienced technical services team, we work with customers across a number of sectors on a wide variety of projects.
Our flexible manufacturing approach allows us to produce pressed metal components in a range of quantity requirements, either on a one off or repeat basis, often to very tight deadlines.
Our skilled team is also able to design and manufacture the necessary tooling for manufacturing pressings from sheets sized up to 900mm x 550mm.
With a dedicated and experienced technical services team, we work with customers across a number of sectors on a wide variety of projects.
Our flexible manufacturing approach allows us to produce pressed metal components in a range of quantity requirements, either on a one off or repeat basis, often to very tight deadlines.
Our skilled team is also able to design and manufacture the necessary tooling for manufacturing pressings from sheets sized up to 900mm x 550mm.
Prototype components are produced on site utilising a range of processes including wire erosion, plunge type EDM and a full range of CNC and conventional machines.
Where appropriate, soft form tooling can also be produced to allow for a low cost and rapid solution.
We can take products from initial prototype right through to full-scale production, providing a complete in-house design and manufacturing service.
Where appropriate, soft form tooling can also be produced to allow for a low cost and rapid solution.
We can take products from initial prototype right through to full-scale production, providing a complete in-house design and manufacturing service.
From these files, we are then able to program the parameters for the milling directly from the 3D drawing and then download the information to the machine.
The benefit to the customer is a quicker processing time and reduced cost.
Customers have taken advantage of this service for rapidly producing prototypes to allow for a complete range of tactile, functionality and strength tests to be quickly carried out.
This service has proved very cost effective as hard tooling and long lead times have been avoided, thus allowing a drastically reduced lead time from design to production volumes.
The benefit to the customer is a quicker processing time and reduced cost.
Customers have taken advantage of this service for rapidly producing prototypes to allow for a complete range of tactile, functionality and strength tests to be quickly carried out.
This service has proved very cost effective as hard tooling and long lead times have been avoided, thus allowing a drastically reduced lead time from design to production volumes.
Reviews
Be the first to review Westcut Engineering.
Write a Review