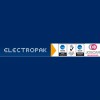
Established in 1986 and with ISO 9001 and AS 9100 Rev D aerospace approvals, our business is focused on manufacturing complete projects with all manufacturing done in house and under our control. Our dedicated and highly skilled staff includes; project managers, machinists, sheet metal workers, welders and painters. Electropak is committed to a culture of continuous improvement with quality and service being the foundation that our business is built upon.
We are thrilled to be working with the epitome of British luxury Aston Martin, supplying busbars for their Valkyrie Hypercar. The carbon fiber material makes the car incredibly lightweight which, combined with the battery-electric system, creates a formidable hybrid. Electropak Ltd are now supplying specialist busbars for space crafts, which must be double insulated through a special process using two different types of insulation.
The insulating materials utilised need to have a low out-gassing profile for use in the vacuum. Our paint treatment facility at our second site now has three environmentally controlled paint booths that have the humidity and temperature controlled at 20°C.
We are thrilled to be working with the epitome of British luxury Aston Martin, supplying busbars for their Valkyrie Hypercar. The carbon fiber material makes the car incredibly lightweight which, combined with the battery-electric system, creates a formidable hybrid. Electropak Ltd are now supplying specialist busbars for space crafts, which must be double insulated through a special process using two different types of insulation.
The insulating materials utilised need to have a low out-gassing profile for use in the vacuum. Our paint treatment facility at our second site now has three environmentally controlled paint booths that have the humidity and temperature controlled at 20°C.
Services
Electropak has assessed capability to ISO 9001 and the aerospace / defence specification AS9100 rev D. We are also an approved supplier to BAE Systems.
As part of our AS9100 rev D KPI's, we are committed to keeping our rejection rate below 0.5% and our on time delivery above 90%.
We are audited on this annually.
We have a fully equipped quality department and inspect parts using a FARO Arm CMM machine.
We are committed to providing quality products and outstanding engineering services to our customers, this is the foundation on which our business is built.
As part of our AS9100 rev D KPI's, we are committed to keeping our rejection rate below 0.5% and our on time delivery above 90%.
We are audited on this annually.
We have a fully equipped quality department and inspect parts using a FARO Arm CMM machine.
We are committed to providing quality products and outstanding engineering services to our customers, this is the foundation on which our business is built.
Our laser and water jet cutting machines give our sheet metal facility the advantage of accuracy and the absence of notch marks.
Precision MIG welding, TIG welding and brazing is carried out by our coded welders.
Our AS9100 rev D approval enables us to weld exotic metals for the aerospace and defence industries.
Our CNC hydraulic press brakes are used to form precision fabricated parts to meet our customer's needs.
We manufacture bespoke tooling in our tool room so that we can form complex shapes.
Precision MIG welding, TIG welding and brazing is carried out by our coded welders.
Our AS9100 rev D approval enables us to weld exotic metals for the aerospace and defence industries.
Our CNC hydraulic press brakes are used to form precision fabricated parts to meet our customer's needs.
We manufacture bespoke tooling in our tool room so that we can form complex shapes.
Our environmentally controlled paint facility is approved to AS9100 rev.
D and by BAE Systems.
We can offer a range of finishes to our fabricated and machined parts.
All parts can be finished in RAL or BS Colours, as well as special military / FED-STD-595 finishes.
Our paint facility has a great reputation for quality and service, with our finished parts go into the aerospace, motorsport and rail industries.
D and by BAE Systems.
We can offer a range of finishes to our fabricated and machined parts.
All parts can be finished in RAL or BS Colours, as well as special military / FED-STD-595 finishes.
Our paint facility has a great reputation for quality and service, with our finished parts go into the aerospace, motorsport and rail industries.
Electropak has a versatile range of CNC milling (3 and 4 axis), CNC turning and grinding machines, which enables us to manufacture precision machined components for a variety of industries such as rail, medical and marine.
Also, our AS9100 rev D approval enables us to manufacture precision components for the aerospace and defence industries.
Our CNC machines receive files electronically allowing us to offer our customers an efficient service and lead time on all our machined components.
We use Autodesk FeatureCAM CNC programming software on all of our CNC machines.
Also, our AS9100 rev D approval enables us to manufacture precision components for the aerospace and defence industries.
Our CNC machines receive files electronically allowing us to offer our customers an efficient service and lead time on all our machined components.
We use Autodesk FeatureCAM CNC programming software on all of our CNC machines.
Our wide range of computerised engraving machines means that we can engrave on all materials including stainless steel for the aerospace industry with our clients including BAE systems.
We are accredited to carry out AS9100 engraving.
Our approvals make us one of a small number of engravers to the military and civil aircraft industries.
The labels, panels and tools that we engrave are for aircraft such as Eurofighter, Tornado, Hawk and the F-35 joint strike fighter.
We also have the facility to do rotary engraving using a 4-axis engraving machine.
We are accredited to carry out AS9100 engraving.
Our approvals make us one of a small number of engravers to the military and civil aircraft industries.
The labels, panels and tools that we engrave are for aircraft such as Eurofighter, Tornado, Hawk and the F-35 joint strike fighter.
We also have the facility to do rotary engraving using a 4-axis engraving machine.
Reviews
Be the first to review Electropak.
Write a Review