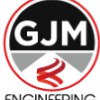
GJM Engineering Ltd has gained an enviable reputation specialising in the design and manufacture of tooling & engineering solutions, providing a responsive engineering service to the Aerospace, Automotive, Defence and Space, Agricultural, Nuclear, oil and gas and sub sea sectors specialising in the design, manufacture and maintenance of details, integrated structures, tooling, special purpose equipment and test equipment.
Based in Deeside, we seek to offer our customers solutions that can meet the needs of the most demanding marketplace. Whether it be a component part or a complex assembly we are committed to producing a high quality product delivered on time, every time and within budget. We seek to offer our customers solutions that can meet the needs of the most demanding marketplace.
In our large project Step changeat Airbus in Broughton, we have been very successfully cooperating with the company GJM since the beginning of assembly on the construction site. With the company GJM we have found a partner here in this project which supports us 100%.
Based in Deeside, we seek to offer our customers solutions that can meet the needs of the most demanding marketplace. Whether it be a component part or a complex assembly we are committed to producing a high quality product delivered on time, every time and within budget. We seek to offer our customers solutions that can meet the needs of the most demanding marketplace.
In our large project Step changeat Airbus in Broughton, we have been very successfully cooperating with the company GJM since the beginning of assembly on the construction site. With the company GJM we have found a partner here in this project which supports us 100%.
Services
GJM Engineering was established in 2008 and is based on a large single site in Deeside.
Over the last few years, GJM have established themselves as a major contributor to the Aerospace & Space, Automotive, medical, nuclear, oil & gas, subsea and Agricultural industries producing total turnkey engineering solutions.
GJM are proud to have employed over 30 local engineers during their recent growth including 6 apprentice engineers.
Our company undertakes full turnkey engineering solutions from concept design to after sales maintenance (PPM) covering tooling design and manufacture across all disciplines including: Airframe Assembly Jigs & Fixtures, Airframe Detail Tooling, Mechanical ground support equipment, access and staging, transportation media, lifting media and test rigs.
Over the last few years, GJM have established themselves as a major contributor to the Aerospace & Space, Automotive, medical, nuclear, oil & gas, subsea and Agricultural industries producing total turnkey engineering solutions.
GJM are proud to have employed over 30 local engineers during their recent growth including 6 apprentice engineers.
Our company undertakes full turnkey engineering solutions from concept design to after sales maintenance (PPM) covering tooling design and manufacture across all disciplines including: Airframe Assembly Jigs & Fixtures, Airframe Detail Tooling, Mechanical ground support equipment, access and staging, transportation media, lifting media and test rigs.
GJM Engineering Design function has an experienced design team.
Our design team are competent in all aspects of tool design, component design, reverse engineering and stress Analysis.
Our Design experience, competence and capability covers all aspects of Tool Design and Flow lines and Automated Robotic Solutions.
These are listed below with some examples of Tools Designed and manufactured by GJM Engineering.
The GJM Engineering website showcases our work carried out for customers worldwide in CNC Machining, Turning, Finishing and Assembly, Fabrication Design and Machinery Manufacture, Metrology and Steel Fabrication.
Our design team are competent in all aspects of tool design, component design, reverse engineering and stress Analysis.
Our Design experience, competence and capability covers all aspects of Tool Design and Flow lines and Automated Robotic Solutions.
These are listed below with some examples of Tools Designed and manufactured by GJM Engineering.
The GJM Engineering website showcases our work carried out for customers worldwide in CNC Machining, Turning, Finishing and Assembly, Fabrication Design and Machinery Manufacture, Metrology and Steel Fabrication.
GJM Fabrication benefits from vast experience in the specialist metal fabrication industry, providing the design and fabrication of metal/alloy products ranging from small precision components to large industrial fabrications.
With over 20 skilled welders, a wide range of modern fabrication equipment in-house including water jetting and plasma cutting, we offer TIG, MIG and ARC coded welding as well as sheet metalwork, forming & bending services.
We are ideally placed to cater for a diverse customer base and accommodate the needs of niche industries including Aerospace, Rail, Defence, Marine & Subsea, Nuclear, and Oil & Gas.
With over 20 skilled welders, a wide range of modern fabrication equipment in-house including water jetting and plasma cutting, we offer TIG, MIG and ARC coded welding as well as sheet metalwork, forming & bending services.
We are ideally placed to cater for a diverse customer base and accommodate the needs of niche industries including Aerospace, Rail, Defence, Marine & Subsea, Nuclear, and Oil & Gas.
Our machine shop capability, capacity and competence has been established over many years.
We have a large machining capacity that has been grown and developed by listening to our customers service requirements and building our CNC capability to meet these needs.
GJM Engineering create process driven CNC machining and manufacturing solutions that satisfy both customer requirements and Industry standards.
We can create a step by step process that will manage your product from concept to final delivery.
We have a large machining capacity that has been grown and developed by listening to our customers service requirements and building our CNC capability to meet these needs.
GJM Engineering create process driven CNC machining and manufacturing solutions that satisfy both customer requirements and Industry standards.
We can create a step by step process that will manage your product from concept to final delivery.
GJM offers powder coating and wet spray painting on steel and aluminium components and small fabrications on site.
Powder coating is based on the principle that objects with opposite electric charges (positive and negative) attract one another.
Powder particles are negatively charged by passing them through a special spraying gun.
This results in an electric field between the spray gun and the earthed component.
The powder particles then follow the field lines and adhere to the product.
The component is then conveyed to an oven where the powder is baked at temperature of 160 to 200 degrees C for approximately 20 minutes.
Powder coating is based on the principle that objects with opposite electric charges (positive and negative) attract one another.
Powder particles are negatively charged by passing them through a special spraying gun.
This results in an electric field between the spray gun and the earthed component.
The powder particles then follow the field lines and adhere to the product.
The component is then conveyed to an oven where the powder is baked at temperature of 160 to 200 degrees C for approximately 20 minutes.
Reviews
Be the first to review GJ Maintenance Engineering.
Write a Review