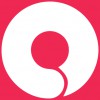
DLR Elastomer Engineering selects materials and combines them with our expert manufacturing knowledge to develop the most suitable processing and fabrication procedure. This ensures that we produce polymer products that are capable of performing in demanding environments. At DLR Elastomer Engineering, we have an extensive range of proprietary and custom-designed polymer products and sheeting.
At DLR Elastomer Engineering, we work closely with clients to understand their needs. We're involved with every stage of the project, from material selection and product development, to prototype testing and manufacturing. At DLR, we work in close collaboration with clients to understand their needs. We support all stages of your project, from initial design and material selection, through to prototype testing, manufacturing and production.
In 2021, DLR Elastomer Engineering Ltd was formed through the successful acquisition and relocation of Elastomer Engineering Ltd into Dexine Leyland Rubber Technology Ltd (DLRT).
At DLR Elastomer Engineering, we work closely with clients to understand their needs. We're involved with every stage of the project, from material selection and product development, to prototype testing and manufacturing. At DLR, we work in close collaboration with clients to understand their needs. We support all stages of your project, from initial design and material selection, through to prototype testing, manufacturing and production.
In 2021, DLR Elastomer Engineering Ltd was formed through the successful acquisition and relocation of Elastomer Engineering Ltd into Dexine Leyland Rubber Technology Ltd (DLRT).
Services
In 2021, DLR Elastomer Engineering Ltd was formed following the successful acquisition and relocation of Elastomer Engineering Ltd into Dexine Leyland Rubber Technology Ltd (DLRT) at our Leyland Facility.
DLRT was formed by the merger of Leyland Rubber Components and Dexine Rubber Technologies, both of which have 100+ years of history as rubber manufacturers.
We are proud to call ourselves experts in the design, development and manufacture of specialised polymer products.
Dexine had a long history dating back to 1895, which included being a key supplier to the War Office.
DLRT was formed by the merger of Leyland Rubber Components and Dexine Rubber Technologies, both of which have 100+ years of history as rubber manufacturers.
We are proud to call ourselves experts in the design, development and manufacture of specialised polymer products.
Dexine had a long history dating back to 1895, which included being a key supplier to the War Office.
DLR combines expansive knowledge of materials, their properties, and processing techniques to develop bespoke mouldings and fabrications for many industry sectors.
Our core services include moulding rubber, rubber sheeting and cast polyurethane products.
We can deliver rubber sheeting with or without fabric inserts.
We can also develop moulded parts with specific properties.
Whilst non-black rubber goods present their challenges, here at DLR, we are equipped to overcome them.
Calendered rubber compound is rotocured with cloth and/or plate finish.
Our core services include moulding rubber, rubber sheeting and cast polyurethane products.
We can deliver rubber sheeting with or without fabric inserts.
We can also develop moulded parts with specific properties.
Whilst non-black rubber goods present their challenges, here at DLR, we are equipped to overcome them.
Calendered rubber compound is rotocured with cloth and/or plate finish.
Polyurethanes (PUs) are in a polymer class of their own.
Polyether or polyester polyurethanes can be made depending on the choice of co-monomers used to produce them.
PUs form a considerable part of the high-performance rubbers and plastics family.
They combine the desired benefits of rigid materials with the elasticity of rubbers, bridging the gap between rubbers and plastics in the many industry sectors served by these versatile polymers.
PU rubber used in our polyurethane casting processes can easily be coloured, unlike regular millable rubbers and still exhibit better abrasion properties.
Polyether or polyester polyurethanes can be made depending on the choice of co-monomers used to produce them.
PUs form a considerable part of the high-performance rubbers and plastics family.
They combine the desired benefits of rigid materials with the elasticity of rubbers, bridging the gap between rubbers and plastics in the many industry sectors served by these versatile polymers.
PU rubber used in our polyurethane casting processes can easily be coloured, unlike regular millable rubbers and still exhibit better abrasion properties.
DLR specialises in providing uncured sheeting in various forms to be fabricated and cured by the client.
Most rubber sheeting is supplied in a cured or vulcanised form, making our rubber sheeting versatile and adaptable.
Application-specific materials are chosen, calendared and supplied on a roll for subsequent fabrication by the client.
In both cases, cured and uncured, woven textile may be inserted to produce the desired properties for parts such as diaphragms, stamped gaskets and conveyor belts, to name a few applications.
Most rubber sheeting is supplied in a cured or vulcanised form, making our rubber sheeting versatile and adaptable.
Application-specific materials are chosen, calendared and supplied on a roll for subsequent fabrication by the client.
In both cases, cured and uncured, woven textile may be inserted to produce the desired properties for parts such as diaphragms, stamped gaskets and conveyor belts, to name a few applications.
Here at DLR Technologies, we have state of the art facilities that enable us to deliver projects to our client's challenging specifications.
From design and development through to manufacturer, we can ensure the highest quality solutions through a whole range of rubber manufacturing capabilities, including rubber calendering and rotocure processes.
Learn more about our facilities and how they benefit each stage of our design and manufacturing processes below.
With design and development completed, the final stage is the manufacture of our products.
From design and development through to manufacturer, we can ensure the highest quality solutions through a whole range of rubber manufacturing capabilities, including rubber calendering and rotocure processes.
Learn more about our facilities and how they benefit each stage of our design and manufacturing processes below.
With design and development completed, the final stage is the manufacture of our products.
Reviews
Be the first to review Elastomer Engineering.
Write a Review