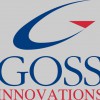
Goss Innovations is a mechanical design engineering consultancy. Specialising in engineering design and analysis, Goss Innovations have a highly skilled team of engineers with a broad range of experience in many fields, including, automotive, aerospace, construction equipment, marine, and special purpose machinery. Goss Innovations Ltd originated in 2000 as a design office to compliment the skills and workforce initiated by Pete Goss for the Team Philips racing catamaran project.
Towards the end of this project, his brother Richard Goss BSc Hons CEng MIAgre, joined as a Director. Bringing to the team his mechanical engineering experience and in depth knowledge of Unigraphics. Goss Innovations has remained in Totnes with Richard as Engineering Director along with his wife as Managing Director establishing themselves as engineering design suppliers to engineering customers in the UK and Europe, in the aerospace, automotive and medical sectors.
Towards the end of this project, his brother Richard Goss BSc Hons CEng MIAgre, joined as a Director. Bringing to the team his mechanical engineering experience and in depth knowledge of Unigraphics. Goss Innovations has remained in Totnes with Richard as Engineering Director along with his wife as Managing Director establishing themselves as engineering design suppliers to engineering customers in the UK and Europe, in the aerospace, automotive and medical sectors.
Services
CAD drives the entire product design process from concept right through development to finished production standard drawings ready for issue.
What many companies miss however are the opportunities for other downstream uses of the CAD data.
Assemblies are built in the CAD system following as closely as possible the way in which they are intended to be manufactured and assembled.
This allows the full use of the CAD data for producing BOMs and analysing fit, function, strength, cost, ease of assembly etc.
What many companies miss however are the opportunities for other downstream uses of the CAD data.
Assemblies are built in the CAD system following as closely as possible the way in which they are intended to be manufactured and assembled.
This allows the full use of the CAD data for producing BOMs and analysing fit, function, strength, cost, ease of assembly etc.
Cost of manufacture should be minimised without compromising the performance of the product.
A detailed understanding of the client's problem is crucial to the building of an effective design specification.
The skills to utilize the latest design tools effectively are pre-requisite to both achieving the best solution as quickly as possible, and to communicating the ideas behind that solution in the most effective way.
Everyone involved needs to fully understand what is being proposed and why.
Enthusiasm, talent, and a belief that almost anything can be improved, helps to drive our team to try to always produce innovative ideas.
A detailed understanding of the client's problem is crucial to the building of an effective design specification.
The skills to utilize the latest design tools effectively are pre-requisite to both achieving the best solution as quickly as possible, and to communicating the ideas behind that solution in the most effective way.
Everyone involved needs to fully understand what is being proposed and why.
Enthusiasm, talent, and a belief that almost anything can be improved, helps to drive our team to try to always produce innovative ideas.
Finite element analysis is a powerful design tool.
Models are built directly from CAD data and analysed to provide estimations of stress strain and deflection under various kinds of loading.
Work is carried out using Inventor Nastran.
These results can be interpreted to give fatigue life predictions of both components and assemblies.
We have a lot of experience using these analysis techniques for design optimisation of highly stressed welded assemblies, leading to cost effective, structurally efficient products.
Models are built directly from CAD data and analysed to provide estimations of stress strain and deflection under various kinds of loading.
Work is carried out using Inventor Nastran.
These results can be interpreted to give fatigue life predictions of both components and assemblies.
We have a lot of experience using these analysis techniques for design optimisation of highly stressed welded assemblies, leading to cost effective, structurally efficient products.
Design and modelling of castings in most materials can be offered.
We have experience of large spheroidal graphite (SG) iron castings used in highly loaded environments often where the casting is being used to replace a fabrication for cost reasons.
Cast steel is another material used in a similar fashion and can be incorporated into welded assemblies.
More specialist materials have also been worked with including aluminium, and titanium.
We have dealt with foundries all over Europe and further afield.
We have experience of large spheroidal graphite (SG) iron castings used in highly loaded environments often where the casting is being used to replace a fabrication for cost reasons.
Cast steel is another material used in a similar fashion and can be incorporated into welded assemblies.
More specialist materials have also been worked with including aluminium, and titanium.
We have dealt with foundries all over Europe and further afield.
Mechanisms form the basis of many of our design solutions.
The ability to simulate designs using CAD and other software is key to optimising a design's performance.
The CAD model can be animated to check for interferences and clearances.
The model can also be used to provide input data to study the loads in all the components to ensure reliable operation of the mechanism.
Mathematical models can be built which allow the effects of variations to the design to be swiftly and accurately assessed.
This is often done in a spreadsheet, which in some cases means the mathematical model can be used to directly drive the CAD model allowing the best appreciation of the problem being solved.
The ability to simulate designs using CAD and other software is key to optimising a design's performance.
The CAD model can be animated to check for interferences and clearances.
The model can also be used to provide input data to study the loads in all the components to ensure reliable operation of the mechanism.
Mathematical models can be built which allow the effects of variations to the design to be swiftly and accurately assessed.
This is often done in a spreadsheet, which in some cases means the mathematical model can be used to directly drive the CAD model allowing the best appreciation of the problem being solved.
Reviews
Be the first to review Goss Innovations.
Write a Review