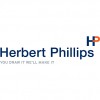
Welcome to Herbert PhillipsHerbert Phillips provides waterjet cutting, venting and ducting, sheet metal work and precision engineering services to discerning customers requiring high quality bespoke work done quickly. Venting and DuctingHerbert Phillips excels at designing and manufacturing lower volume bespoke venting and ducting systems and products where quality and speed of turnaround are paramount.
Take the Mach 2, the world's most powerful waterjet cutter, add two very experienced operators, and you've got one of the best waterjet cutting services in the region. Trusted by leading companies like Lindab to manufacture high-quality 'specials' and 'one-offs', we are the ideal choice for high quality bespoke solutions with fast turnarounds.
For low-volume specialist sheet metal work jobs Herbert Phillips is a very safe pair of hands because each project is carefully managed by an experienced sheet metal work specialist.Herbert Phillips offer customers a fully managed CNC milling and CNC turning service incorporating manufacturing design, prototyping, testing, part-assembly and delivery.
Take the Mach 2, the world's most powerful waterjet cutter, add two very experienced operators, and you've got one of the best waterjet cutting services in the region. Trusted by leading companies like Lindab to manufacture high-quality 'specials' and 'one-offs', we are the ideal choice for high quality bespoke solutions with fast turnarounds.
For low-volume specialist sheet metal work jobs Herbert Phillips is a very safe pair of hands because each project is carefully managed by an experienced sheet metal work specialist.Herbert Phillips offer customers a fully managed CNC milling and CNC turning service incorporating manufacturing design, prototyping, testing, part-assembly and delivery.
Services
To be instrumental in the success of our client's projects by providing a service that surpasses their expectations in terms of product quality, speed of delivery, cost and efficiency.
We are a manufacturing and fabrication business owned and managed by Adam Phillips with Andrew Jones managing manufacturing operations at Toddington.
Andrew has over 30 years' manufacturing experience and is regarded as one of the leading sheet metalwork specialists in the UK.
Stephen Williams is assistant manager at our Toddington facility.
We are a manufacturing and fabrication business owned and managed by Adam Phillips with Andrew Jones managing manufacturing operations at Toddington.
Andrew has over 30 years' manufacturing experience and is regarded as one of the leading sheet metalwork specialists in the UK.
Stephen Williams is assistant manager at our Toddington facility.
Waterjet cutting is fast, accurate, versatile and cost effective.
The Herbert Phillips Mach 2 is the world's most powerful waterjet cutter and can cut through virtually any material.
Our Mach 2 waterjet cutter based at our unit in Toddington, Cheltenham Gloucestershire is able to cut detailed patterns accurately in virtually any material up to a thickness of 150mm.
The quality of the cut is so good that further machining processes can be eliminated thus saving your business money.
Our Mach 2 waterjet cutting service is better than other cutting services such as laser and plasma.
The Herbert Phillips Mach 2 is the world's most powerful waterjet cutter and can cut through virtually any material.
Our Mach 2 waterjet cutter based at our unit in Toddington, Cheltenham Gloucestershire is able to cut detailed patterns accurately in virtually any material up to a thickness of 150mm.
The quality of the cut is so good that further machining processes can be eliminated thus saving your business money.
Our Mach 2 waterjet cutting service is better than other cutting services such as laser and plasma.
Materials such as titanium, Inconel, tool steel and brass are highly valuable, yet their resilient composition makes them tough to cut.
Thankfully, there is an effective solution: abrasive waterjet cutting.
The waterjet cutting process employs a high-speed, high-pressure jet of water to cut through material in high or low volumes and from 1/16" to 8" in thickness.
As well as cutting with supreme accuracy and leaving clean edges every time, waterjet cutting also requires no tool sharpening.
It causes no stress impact, heat distortion or heat- affected zones either, so there is rarely any need for secondary cutting.
Thankfully, there is an effective solution: abrasive waterjet cutting.
The waterjet cutting process employs a high-speed, high-pressure jet of water to cut through material in high or low volumes and from 1/16" to 8" in thickness.
As well as cutting with supreme accuracy and leaving clean edges every time, waterjet cutting also requires no tool sharpening.
It causes no stress impact, heat distortion or heat- affected zones either, so there is rarely any need for secondary cutting.
Glass is one of the most versatile and useful of substances available, and windows, mirrors, ornaments and tabletops are just some of the everyday products that are made from it.
Yet its structure makes it difficult to cut without damage and wastage, as even the smallest scratch can lead to fractures on the surface.
A waterjet cuts glass through the combination of an ultra-fine kerf and extremely high pressure.
Therefore you don't need to etch and break when you cut glass with a waterjet, which means less wasted glass and, ultimately, more profits for your business.
Yet its structure makes it difficult to cut without damage and wastage, as even the smallest scratch can lead to fractures on the surface.
A waterjet cuts glass through the combination of an ultra-fine kerf and extremely high pressure.
Therefore you don't need to etch and break when you cut glass with a waterjet, which means less wasted glass and, ultimately, more profits for your business.
Waterjet cutting can be used on a wide variety of plastics and the results are far superior to those of other cutting methods.
This is largely down to the waterjet cutter's fine but immensely powerful jet which achieves clean edges every time.
One of the major drawbacks to more traditional plastic-cutting techniques is the fact that the cutters tend to bind with the material due to the heat involved in the process.
Other problems include stringy swarf and tools wearing out quickly.
These drawbacks do not occur when using our waterjet cutting service - instead you get burr-free cuts with little mess or wastage.
This is largely down to the waterjet cutter's fine but immensely powerful jet which achieves clean edges every time.
One of the major drawbacks to more traditional plastic-cutting techniques is the fact that the cutters tend to bind with the material due to the heat involved in the process.
Other problems include stringy swarf and tools wearing out quickly.
These drawbacks do not occur when using our waterjet cutting service - instead you get burr-free cuts with little mess or wastage.
Reviews
Be the first to review Herbert Phillips.
Write a Review